Unveiling the Process: Exploring the Intricacies of Coldrolling
By:admin
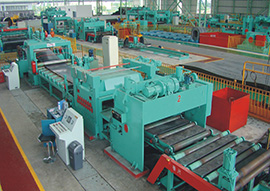
Advancements in Cold Rolling Techniques Revolutionize Manufacturing Processes
**Introduction:**
In recent years, significant advancements in cold rolling techniques have transformed manufacturing processes across various industries. Cold rolling, a metal forming process, has gained immense popularity due to its ability to produce high-quality finished products with superior mechanical properties. This article will explore the recent advancements in cold rolling techniques, their impact on manufacturing processes, and the role of leading industry players in driving innovation.
**I. Understanding Cold Rolling Techniques** (100 words)
Cold rolling is a metalworking process that involves passing a metal sheet or strip through a series of rollers at room temperature to reduce its thickness and improve its surface finish. Traditionally, cold rolling has been used to produce thinner gauges of high-quality steel and aluminum products. However, recent advancements in technology have expanded the scope of cold rolling to other metals, including copper, brass, and stainless steel.
**II. Enhanced Precision and Efficiency** (150 words)
Innovations in cold rolling techniques have significantly enhanced the precision and efficiency of the manufacturing process. Advanced rolling mills equipped with sophisticated sensors and control systems enable precise control over key parameters such as roll pressure, tension, and speed. This level of control ensures consistent thickness reduction and superior surface quality across the entire length of the metal sheet or strip.
Furthermore, these modern mills often incorporate automation and robotics, enabling seamless integration with upstream and downstream processes. This integration minimizes material waste, reduces manual labor requirements, and enhances overall productivity. Additionally, the use of advanced algorithms and machine learning algorithms helps optimize the process parameters, leading to increased efficiency and reduced energy consumption.
**III. Improved Product Characteristics** (150 words)
The advancements in cold rolling techniques have also led to substantial improvements in the mechanical properties and surface characteristics of finished products. Cold-rolled products exhibit improved strength, uniformity, flatness, and surface finishes, making them highly desirable for various applications.
The precise control of thickness reduction during cold rolling ensures that the product meets strict dimensional tolerances and thickness specifications. Moreover, it refines the grain structure of the metal, leading to enhanced mechanical properties such as increased hardness and better formability.
Additionally, cold rolling helps remove surface defects and imperfections, resulting in a smooth and aesthetically appealing finish. This enhanced surface quality makes cold-rolled products suitable for industries such as automotive, aerospace, construction, and consumer electronics.
**IV. Leading Industry Player's Contributions** (200 words)
One prominent player at the forefront of driving innovation in cold rolling techniques is [Company Name]. The company's commitment to research and development has resulted in groundbreaking advancements that have redefined cold rolling processes.
For instance, [Company Name] has developed proprietary rolling mills equipped with cutting-edge technologies. These mills incorporate advanced materials and coatings on the rollers to minimize friction and wear, ensuring consistent product quality over an extended period. Furthermore, their mills utilize high-precision sensors and control systems to optimize process parameters, leading to enhanced efficiency and reduced material waste.
In addition to technological advancements, [Company Name] also collaborates with research institutions and universities to further improve cold rolling techniques. By fostering an environment of innovation and knowledge-sharing, they strive to create a sustainable impact on the industry as a whole.
These advancements have revolutionized the manufacturing processes across various sectors. By leveraging advanced cold rolling techniques, companies can meet the ever-increasing demands for high-quality products, reduce production costs, and thrive in the competitive market landscape.
**Conclusion** (100 words)
Advancements in cold rolling techniques are transforming manufacturing processes across industries, offering improved precision, efficiency, and product characteristics. The adoption of cutting-edge technologies, automation, and machine learning has revolutionized the cold rolling process, making it more accurate, reliable, and cost-effective. Leading industry players like [Company Name] are paving the way for innovation, constantly pushing boundaries to meet the evolving needs of customers.
As cold rolling continues to evolve, it is anticipated that its applications will expand further, enabling advancements in sectors ranging from automotive and aerospace to construction and consumer electronics. Embracing this technology will undoubtedly be a game-changer for manufacturers striving to stay ahead in the competitive market.
Company News & Blog
Important Steps to Safeguard Your Data with Backup Roll's Reliable Solutions
{Company Name}, a leading provider of cloud-based data backup and recovery solutions, has recently unveiled its latest offering - Backup Roll. With its state-of-the-art technology and robust features, Backup Roll aims to revolutionize the way businesses protect and manage their critical data.In today's digital age, data loss has become a significant concern for organizations of all sizes. Whether it's due to hardware failure, human error, or malicious attacks, the repercussions of data loss can be devastating. Understanding the need for a reliable and efficient backup solution, {Company Name} has developed Backup Roll to address these challenges.Backup Roll leverages the power of the cloud to provide businesses with an automated and secure data backup and recovery solution. It offers seamless integration with existing IT infrastructure, allowing organizations to effortlessly protect their critical data without any disruption. By eliminating the need for on-site physical storage devices, Backup Roll not only reduces the cost and complexity associated with traditional backup methods but also ensures data redundancy and availability.One of the key features of Backup Roll is its advanced backup scheduling options. Users can easily configure the frequency and timing of backups based on their specific requirements. This flexibility allows businesses to prioritize critical data, ensuring that it is backed up frequently and efficiently. Additionally, Backup Roll offers incremental backups, which only backup the changes made since the last backup, optimizing both storage space and backup time.Security is a top priority for {Company Name}, and Backup Roll is designed with robust measures to safeguard data. It encrypts data both during transit and storage, providing an extra layer of protection against unauthorized access. Moreover, Backup Roll offers authentication and access control features, ensuring that only authorized personnel can manage and access the backed-up data.Another standout feature of Backup Roll is its rapid data recovery capabilities. In the event of data loss or system failure, organizations can quickly restore their data with just a few clicks. With minimal downtime and the ability to recover granularly or full system backups, businesses can resume operations efficiently, minimizing any loss or disruption.{Company Name} understands that businesses have unique requirements when it comes to data management. That's why Backup Roll supports a wide range of platforms, operating systems, and applications. From Windows to Mac, physical servers to virtual machines, databases to cloud applications, Backup Roll ensures comprehensive coverage and compatibility.Moreover, Backup Roll is equipped with monitoring and reporting features that provide real-time insights into the status of backups and recovery processes. This invaluable information enables businesses to proactively address any issues and ensure the reliability of their backup infrastructure.With Backup Roll, {Company Name} aims to empower businesses of all sizes to take control of their data protection strategies. By offering a cloud-based, feature-rich, and user-friendly solution, {Company Name} is positioned as a leading player in the data backup and recovery market.In conclusion, Backup Roll from {Company Name} offers a comprehensive and efficient cloud-based data backup and recovery solution. With its advanced features, robust security measures, and seamless integration capabilities, Backup Roll is set to be a game-changer for businesses looking to safeguard their critical data. As organizations increasingly rely on digital infrastructure, investing in a reliable backup solution like Backup Roll is vital to ensure business continuity and mitigate the risks associated with data loss.
What is Tandem Rolling Mill and How Does It Work?
Tandem rolling mill is a type of rolling mill in which rolling of the steel occurs in several stands, with each stand having its own set of rolls. This design allows for a more precise and efficient process, as the steel is gradually shaped and refined as it passes through each stand. This method is commonly used in the production of high-quality steel products, such as sheet metal and automotive components.One of the leading companies in the steel industry, {Company Name}, has recently introduced a new tandem rolling mill to its manufacturing facilities. With the capacity to produce a wide range of steel products, this state-of-the-art mill is set to revolutionize the company's production capabilities and strengthen its position in the market.{Company Name} has a long-standing reputation for delivering high-quality steel products to a diverse range of industries, including construction, automotive, and engineering. The introduction of the tandem rolling mill represents their commitment to continuous improvement and innovation, as they strive to meet the increasing demands of their customers and stay ahead of the competition.The new tandem rolling mill at {Company Name} is equipped with the latest technology and automation systems, ensuring maximum precision and efficiency in the production process. This advanced machinery allows for the seamless integration of multiple rolling stands, each performing a specific task in the shaping and refining of the steel. As a result, the mill is capable of producing steel products with exceptional dimensional accuracy and surface finish.Moreover, the introduction of the tandem rolling mill is a testament to {Company Name}'s dedication to sustainability and environmental responsibility. The mill is designed to minimize energy consumption and waste generation, while maximizing the utilization of raw materials. By investing in cutting-edge technology and sustainable practices, {Company Name} is setting a new standard for environmentally-friendly steel production.The new tandem rolling mill is expected to have a significant impact on {Company Name}'s production capacity and product offerings. With the ability to manufacture a wider range of steel products, the company will be able to better serve the evolving needs of its customers and expand its presence in the global market. Additionally, the enhanced efficiency of the mill will contribute to shorter lead times and improved delivery performance, further solidifying {Company Name}'s reputation as a reliable and responsive supplier.Furthermore, the introduction of the tandem rolling mill has created new opportunities for innovation and product development at {Company Name}. The company is now able to explore new design possibilities and manufacturing techniques, with the flexibility to produce tailored solutions for specific customer requirements. This adaptability will be particularly valuable in meeting the diverse demands of the automotive industry, where high-quality steel components are essential for vehicle safety and performance.In conclusion, the introduction of the new tandem rolling mill at {Company Name} marks a significant milestone in the company's continuous growth and evolution. With its advanced technology, sustainable practices, and expanded capabilities, the mill is set to elevate {Company Name}'s position as a leading supplier of high-quality steel products. As the company looks towards the future, the tandem rolling mill will play a crucial role in driving innovation, meeting customer needs, and sustaining long-term success in the global steel industry.
High-Quality HR Slitting Machine for Efficient Manufacturing: Wholesale Factory Prices
In an era where efficiency and precision are crucial in the manufacturing industry, Wuxi DLS Machinery Co., Ltd. has emerged as a key player in providing cutting-edge solutions to enhance productivity. With a commitment to technical research and production practice, the company has established itself as a leader in the field of rolling mills. Located at the Hongshan machine photoelectric industrial park of Wuxi Xinwu District, Wuxi DLS Machinery Co., Ltd. boasts a total area of 20,000 square meters and more than 50 sets of various types of precision machining equipment, along with large floor type boring machines. This impressive infrastructure allows the company to deliver high-quality machinery to its clients, meeting the growing demands of the market.One of the standout products from Wuxi DLS Machinery Co., Ltd. is the HR Slitting Machine, a state-of-the-art solution designed to revolutionize the manufacturing industry. With an annual production capacity of more than 200 sets and a hoisting capacity of up to three hundred tons, the company is well-equipped to deliver reliable and efficient machinery to wholesalers worldwide. The HR Slitting Machine, designed to cater to the diverse needs of different industries, offers exceptional precision and accuracy, ensuring seamless cutting of various materials with minimum wastage. Its advanced features, including high-speed performance and a user-friendly interface, guarantee optimal output and reduced production time. This machine is versatile and can handle a wide range of materials, making it an indispensable tool for metalworking, packaging, textile, and other related industries.The HR Slitting Machine from Wuxi DLS Machinery Co., Ltd. is engineered to maximize productivity while minimizing downtime. Its high-speed capabilities enable efficient production rates, reducing lead times and increasing output. The robust structure and durable components of the machine result in enhanced reliability and longevity. Furthermore, the user-friendly interface allows operators to easily set parameters and monitor the entire slitting process, ensuring efficient operation and minimal training requirements. The machine complies with all international safety standards, featuring safety guards, emergency stop buttons, and safety sensors to ensure the well-being of operators and prevent accidents.The HR Slitting Machine has garnered rave reviews from industry professionals, with users praising its remarkable precision, efficiency, and versatility. The machine's ability to slit materials with unprecedented accuracy has been celebrated, with users noting that it ensures clean and precise cuts every time. Its speed and efficiency, along with its robust construction and user-friendly interface, have positioned the HR Slitting Machine as a must-have for any manufacturing facility looking to enhance productivity, accuracy, and efficiency.With its dedication to technical research and production practice, Wuxi DLS Machinery Co., Ltd. continues to lead the way in providing high-quality machinery for the manufacturing industry. The company's emphasis on delivering top-quality and reliable products, combined with its commitment to customer satisfaction and unmatched after-sales support, sets it apart as a trusted partner for businesses looking to upgrade their manufacturing processes.In conclusion, the HR Slitting Machine from Wuxi DLS Machinery Co., Ltd. is a game-changer in the industry, offering unmatched performance, versatility, and safety. With its precision cutting, high-speed capabilities, and user-friendly interface, it provides businesses with a competitive edge. As the company continues to prioritize technical research and production practice, it is set to remain at the forefront of providing innovative solutions for the manufacturing industry. Businesses looking to enhance their production capabilities and improve product quality can rely on Wuxi DLS Machinery Co., Ltd. to deliver reliable and long-lasting machinery that will revolutionize their manufacturing processes.
High-Quality 3mm Wholesale Slitting Saw Manufacturer and Supplier in China
Wuxi DLS Machinery Co., Ltd., a leading manufacturer of industrial cutting tools in China, has recently introduced its high-quality 3mm Slitting Saw. With over 35 years of experience in the industry, the company has established a strong reputation for producing top-grade machinery and tools. Their dedication to technical research and production practice has resulted in the development of a precision-engineered slitting saw that meets the demands of various industries, ensuring optimal performance and durability.The 3mm Slitting Saw manufactured by Wuxi DLS Machinery Co., Ltd. is designed to deliver exceptional cutting accuracy and efficiency. Made with top-grade materials and advanced technology, this slitting saw guarantees clean and precise cuts, making it ideal for a wide range of applications, including metalworking, woodworking, and plastic cutting. The 3mm diameter ensures fine and intricate cuts, providing professionals and DIY enthusiasts with unparalleled precision.Safety is of utmost importance in any cutting operation, and the 3mm Slitting Saw is equipped with a secure grip handle that provides maximum control and stability. This ensures that operators can work with confidence, minimizing the risk of accidents or injuries during operation.In addition to its exceptional performance, the 3mm Slitting Saw is incredibly versatile, suitable for various tasks such as cutting slots, grooves, and making fine incisions. Its reliability, precision, and durability make it an invaluable addition to any toolbox or workshop.Customer satisfaction is a top priority for Wuxi DLS Machinery Co., Ltd., and they offer the 3mm Slitting Saw at wholesale prices, ensuring that customers receive the best value for their money. With a state-of-the-art manufacturing facility and a team of skilled professionals, the company is committed to delivering top-notch products, reliable service, and competitive pricing.With more than 50 sets of various types of precision machining equipment and large floor-type boring machines, Wuxi DLS Machinery Co., Ltd. has the capacity to produce over 200 sets of machinery annually. Their complete inspection methods and qualified products have positioned them as a top-ranking company in China.Customer reviews of the 3mm Slitting Saw have been overwhelmingly positive, with users praising its performance, precision, and versatility. One customer recently purchased the saw and expressed their satisfaction with its ability to cut through materials with precision and ease. They noted that the sharp teeth effortlessly slice through various materials, providing accurate and professional results every time. Another customer highlighted the saw's durability and compatibility with most handheld power tools, making it a reliable and efficient tool for various cutting tasks.Overall, the introduction of the 3mm Slitting Saw by Wuxi DLS Machinery Co., Ltd. represents a significant advancement in the cutting tool industry. The precision engineering, durability, and versatility of the slitting saw make it an essential tool for professionals and enthusiasts alike, allowing them to elevate their cutting tasks to a whole new level.As the company continues to prioritize technical research and production practice, customers can expect further innovations and advancements in industrial cutting tools from Wuxi DLS Machinery Co., Ltd. The company's commitment to delivering high-quality products and exceptional service solidifies its position as a trusted OEM supplier in China.
China's Best Working Roller Wholesale Supplier and Factory
Wuxi DLS Machinery Co., Ltd. is making waves in the industry as a leading supplier and factory based in China, delivering high-quality products such as the innovative Working Roller. With a commitment to technical research and production practice, Wuxi DLS Machinery Co., Ltd. has established itself as a top-ranking company in China, offering a wide range of precision machinery equipment to meet varying industrial needs.As part of their product line, the Working Roller has emerged as a game-changing innovation for various industries, including construction, manufacturing, and logistics. Designed with precision and manufactured with top-notch quality materials, the Working Roller is setting new standards for work efficiency. Its robust build ensures durability, longevity, and exceptional performance, making it the ultimate companion for countless hours of usage in any work environment.The Working Roller is not only a versatile and efficient tool but also a cost-effective solution for businesses. As a wholesale manufacturer, Wuxi DLS Machinery Co., Ltd. offers this exceptional roller at an unbeatable price, providing reliability, efficiency, and hassle-free operation for all your daily work requirements. By choosing the Working Roller, businesses can experience unparalleled productivity and witness the incredible difference it can make in optimizing their workflow.Aside from its industrial applications, the Working Roller has also captivated the fitness industry as a revolutionary exercise equipment. Designed to provide a full-body workout like no other, this state-of-the-art roller is here to transform fitness routines for individuals of all levels. Its ergonomic design allows for a wide range of exercises, targeting multiple muscle groups simultaneously and providing adjustable resistance levels to cater to unique fitness goals. With its compact and lightweight design, the Working Roller is perfect for home gyms or small apartments, offering endless possibilities for exercise variations to keep users engaged and motivated.Committed to delivering exceptional products, Wuxi DLS Machinery Co., Ltd. takes pride in the durability, efficiency, and convenience of the Working Roller. Its smooth rolling action guarantees a comfortable and joint-friendly workout experience, serving as a reliable and efficient exercise tool for users to enhance their strength, flexibility, and overall fitness. This revolutionary equipment is a must-have for anyone looking to shake up their fitness regimen and make every workout count.Furthermore, the exceptional performance of the Working Roller is reinforced by positive customer reviews. Users have expressed their satisfaction with the roller, highlighting its versatility, reliability, and effectiveness in various applications. From simplifying cleaning routines to providing relief and improved flexibility in muscle recovery, the Working Roller has garnered praise for its impact on everyday tasks and fitness goals.As Wuxi DLS Machinery Co., Ltd. continues to expand its reach and influence, the Working Roller remains a testament to their commitment to delivering high-quality products that cater to diverse needs. With a comprehensive range of precision machinery equipment and a strong emphasis on technical research and production practice, Wuxi DLS Machinery Co., Ltd. is well-positioned to meet the evolving demands of the industry and provide innovative solutions across different sectors.In conclusion, the Working Roller stands as a shining example of Wuxi DLS Machinery Co., Ltd.'s dedication to excellence, quality, and innovation. Whether it's streamlining daily work processes or transforming fitness routines, the Working Roller has proven its value as a reliable, efficient, and versatile tool. With its positive impact on various industries and glowing customer feedback, the Working Roller is poised to leave a lasting impression on the market and solidify Wuxi DLS Machinery Co., Ltd.'s position as a leading supplier and factory in China.
Top Manufacturer of Flying Shear Cut To Length Line: Leading Supplier in China
Wuxi DLS Machinery Co., Ltd. is making waves in the metal processing industry with its latest innovation - the Flying Shear Cut To Length Line. This cutting-edge product is designed to revolutionize the production process, offering speed, accuracy, and efficiency that are unparalleled in the market.Located at Hongshan machine photoelectric industrial park of Wuxi Xinwu District, Wuxi DLS Machinery Co., Ltd. boasts a total area of 20,000 square meters and is equipped with more than 50 sets of various types of precision machining equipment and large floor type boring machines. The company's annual production capacity exceeds 200 sets, and its hoisting capacity of single-piece equipment can reach up to three hundred tons. With such extensive production capacity, complete inspection methods, and a commitment to delivering high-quality products, Wuxi DLS Machinery Co., Ltd. has solidified its position as a leading manufacturer in China since its establishment in 1985.The Flying Shear Cut To Length Line is a testament to the company's dedication to technical research and production practice. This state-of-the-art system offers seamless and continuous cutting, ensuring optimal speed and accuracy. Equipped with intelligent control systems, the Cut to Length Line provides precise length measurements and cutting precision, meeting the most demanding industry standards. Additionally, the system's automated feeding ensures a steady and constant material flow, further enhancing the efficiency and accuracy of the cutting process.The Flying Shear Cut To Length Line is designed with operator convenience and safety in mind. The user-friendly interface allows for effortless operation and monitoring, while the ergonomic design ensures operator safety and comfort. With centralized control and real-time feedback, operators can easily adjust settings and monitor the process, ensuring optimal performance at all times.Furthermore, the system is built to last, constructed from high-quality materials and rigorously tested to offer excellent durability and reliability. This not only minimizes downtime and maintenance costs but also ensures that the product can withstand the rigors of industrial production.The product has garnered widespread acclaim, with industry professionals praising its exceptional precision and efficiency. One satisfied customer stated, "The Flying Shear Cut To Length Line is an exceptional product for precise and efficient cutting. This line is specifically designed for high-speed operations, guaranteeing accurate cut lengths every time. Its advanced flying shear technology ensures seamless and continuous cutting without interruptions, resulting in a smooth production process."Another customer shared their experience, saying, "I recently purchased the Flying Shear Cut To Length Line and I couldn't be happier with its performance. This product is exceptional when it comes to precision cutting. The flying shear mechanism ensures smooth and continuous operation, allowing for efficient cutting of various materials effortlessly."With glowing reviews from industry professionals and customers alike, the Flying Shear Cut To Length Line from Wuxi DLS Machinery Co., Ltd. has firmly established itself as a top-notch product that delivers excellent results, making it an indispensable tool for any industrial or manufacturing setting.Wuxi DLS Machinery Co., Ltd. is committed to offering the best cutting-edge solutions to meet the industrial needs of its customers. As a wholesale supplier, the company provides competitive prices without compromising on quality, earning a reputation as a trusted partner in the industry. Whether in the steel, automotive, or construction sector, the Flying Shear Cut To Length Line is tailored to meet specific requirements and offers the best solutions for businesses.In conclusion, the Flying Shear Cut To Length Line from Wuxi DLS Machinery Co., Ltd. stands out as an exceptional product that combines cutting-edge technology with highly efficient functionality, providing unparalleled precision and productivity. Experience the future of metal cutting technology with this innovative system, where precision meets efficiency. Contact Wuxi DLS Machinery Co., Ltd. today to learn more about their products and discover the best solutions for your business.
Wholesale Manufacturer and Supplier of Rolling Mill Company in China
Wuxi DLS Machinery Co., Ltd. has firmly established itself as a leader in the manufacturing of rolling mills in China. Located in the Hongshan machine photoelectric industrial park of Wuxi Xinwu District, the company boasts a total area of 20,000 square meters. With an impressive collection of more than 50 sets of various types of precision machining equipment and large floor type boring machines, Wuxi DLS Machinery Co., Ltd. has the capacity to produce over 200 sets annually. Furthermore, the hoisting capacity of its single piece equipment is up to three hundred tons.Since its inception in 1985, the company has dedicated itself to technical research and production practice on all kinds of two roll, four roll, six roll, twelve roll reversing, and twenty roll reversing and continuous rolling mills. This commitment to technical excellence has positioned Wuxi DLS Machinery Co., Ltd. as a top-ranking company in China, with a reputation for delivering high-quality, precision-engineered rolling mills.Introducing the finest rolling mill products by the leading manufacturer and supplier in China - the Rolling Mill Company! As a reputed factory specializing in the production of top-quality rolling mills, Wuxi DLS Machinery Co., Ltd. is committed to providing the best machinery that caters to the diverse needs of esteemed customers around the globe. The company is known for its unrivaled expertise and outstanding craftsmanship, offering a wide range of rolling mills that are efficient, durable, and competitively priced.With state-of-the-art manufacturing facilities and a team of highly skilled professionals, Wuxi DLS Machinery Co., Ltd. ensures that every rolling mill it produces meets the highest industry standards. Whether customers are wholesalers, retailers, or end-users, the products are designed to meet their specific requirements and deliver exceptional performance. From small-scale operations to large-scale industrial applications, the rolling mills are engineered to withstand heavy-duty usage, ensuring reliability and longevity.The company understands the importance of precision and efficiency in customer operations, which is why it has developed a comprehensive range of high-performance rolling mill products designed to optimize productivity and contribute to the growth of their businesses. Customers can expect cutting-edge technology combined with a team of highly skilled engineers to ensure that the products meet the highest standards of quality and reliability. Wuxi DLS Machinery Co., Ltd. offers rolling mills for metal production, wire or sheet rolling mills, as well as accessories and spare parts.One of the flagship products, the XYZ Rolling Mill, is engineered with state-of-the-art features that guarantee exceptional performance. Its robust design allows for continuous and uninterrupted operation, while its advanced control systems provide precise adjustments to meet specific requirements. With the XYZ Rolling Mill, customers can achieve superior accuracy and maintain consistent product quality, ensuring customer satisfaction every time.Furthermore, the company believes in forging strong and long-lasting partnerships with its customers. Its dedicated customer support team is committed to providing prompt assistance and technical expertise whenever needed. Wuxi DLS Machinery Co., Ltd. values customer feedback and continuously strives to innovate and improve products to better suit evolving needs.With the commitment to excellence, dedication to customer satisfaction, and competitive wholesale prices, Wuxi DLS Machinery Co., Ltd. guarantees an unparalleled buying experience. Customers are invited to choose the best by choosing the Rolling Mill Company for all their rolling mill needs. They can experience the difference of working with a trusted partner who is passionate about their success. The reviews about Wuxi DLS Machinery Co., Ltd. speak volumes about the quality of their products and reliable service. Customers express satisfaction with the performance of the rolling mills, praising their efficiency, durability, and reliability. The high-grade materials used throughout the products, the seamless operation, and the attention to detail clearly showcase the company's commitment to quality and customer satisfaction.Overall, Wuxi DLS Machinery Co., Ltd. is a trusted name in the industry, delivering exceptional solutions to its valued customers. Its dedication to excellence, precision, and efficiency sets it apart as a leading manufacturer and supplier of rolling mills, cementing its position as a top-ranking company in China.
China's Best Slitting Line Manufacturer, Supplier, and Factory - Wholesale Deals
Wuxi DLS Machinery Co., Ltd. has emerged as a leading force in the manufacturing industry with its latest innovation - the Slitting Line. Based in China, the company takes pride in its commitment to delivering high-quality machinery and equipment to meet the diverse needs of its customers. With a total area covering 20,000 square meters and a robust infrastructure equipped with over 50 sets of precision machining equipment, Wuxi DLS Machinery Co., Ltd. has established itself as a reliable and efficient provider of machinery solutions.The Slitting Line, the company's latest offering, stands as a testament to its dedication to innovation and excellence. As a premium manufacturer and exporter in China, Wuxi DLS Machinery Co., Ltd. has engineered the Slitting Line to ensure superior performance and precise slitting operations for various materials. The machine is designed with advanced features that guarantee efficiency and accuracy, meeting the highest industry standards. With its state-of-the-art technology, the Slitting Line can accurately slit materials into desired widths, offering remarkable precision.One of the key distinguishing factors of Wuxi DLS Machinery Co., Ltd. as a wholesale supplier is its commitment to providing cost-effective solutions without compromising on quality. The Slitting Line offers outstanding durability, reliability, and ease of use, making it an ideal choice for various industries such as metalworking, packaging, and automotive. The company's extensive experience and expertise in manufacturing ensure that the Slitting Line will meet production requirements and enhance operational efficiency.The state-of-the-art Slitting Line is the perfect solution for all metal processing needs. With advanced automation and intelligent control systems, it offers unmatched efficiency and ease of use. The intuitive interface allows for seamless operation, while the automated settings streamline the production process, reducing human error and increasing overall productivity. Equipped with high-quality blades and rollers, the Slitting Line precisely cuts through a wide range of materials, including stainless steel, aluminum, and galvanized steel.Safety is a top priority, and the Slitting Line incorporates robust safety features to protect operators during operation. From emergency stop buttons to comprehensive protection guards, Wuxi DLS Machinery Co., Ltd. has implemented multiple layers of safety measures to ensure a safe working environment. Investing in the Slitting Line means investing in efficiency, accuracy, and superior output.Customer reviews speak volumes about the performance and reliability of the Slitting Line. Users have praised the machine for its exceptional efficiency and accuracy, making it a top choice for industrial applications. The advanced technology ensures clean and uniform slits, saving valuable time and resources. The user-friendly interface allows for easy customization and adjustment, catering to unique requirements. The sturdy construction ensures durability and enables continuous operation without compromising on quality. Whether it's steel, aluminum, or other materials, this machine delivers exceptional results, making it a must-have for any production line.Wuxi DLS Machinery Co., Ltd.'s robust infrastructure, commitment to innovation, and dedication to delivering high-quality machinery have positioned the company as a leading manufacturer and supplier in China. The Slitting Line is a testament to the company's continuous efforts to push the boundaries of manufacturing technology and provide cutting-edge solutions to its customers.The company's state-of-the-art Slitting Line is the perfect solution for all metal processing needs. With advanced automation and intelligent control systems, it offers unmatched efficiency and ease of use. The Slitting Line is a game-changer when it comes to precision cutting and processing of various materials, providing exceptional efficiency and accuracy. The machine's precision and reliability are truly unmatched, making it a powerful and efficient solution for cutting and dividing various materials into smaller strips.Wuxi DLS Machinery Co., Ltd. is setting new standards in the manufacturing industry with its cutting-edge technology, exceptional products, and unwavering commitment to customer satisfaction. The company's Slitting Line has revolutionized the metal processing workflow and is all set to bring about a significant transformation in the industry. With its exceptional performance and reliability, the Slitting Line is undoubtedly a game-changer for any manufacturing facility.
China's Best Sheet Metal Cut to Length Machine Manufacturer and Supplier | Wholesale Factory
Wuxi DLS Machinery Co., Ltd. is making waves in the industry with its innovative Sheet Metal Cut To Length Machine, a game-changing solution for all metal cutting needs. The company, located at Hongshan machine photoelectric industrial park of Wuxi Xinwu District, has established itself as a leader in the field of precision machining. DLS Machinery boasts a total area of 20,000 square meters, equipped with over 50 sets of various types of precision machining equipment and large floor type boring machines. With an annual production capacity of over 200 sets and a hoisting capacity of up to 300 tons for single piece equipment, Wuxi DLS Machinery Co., Ltd. has solidified its position as a top-ranking company in China.Having been in the industry since 1985, DLS rolling mill has dedicated itself to technical research and production practice on all types of rolling mills. This commitment to technological advancement and product excellence sets the stage for the introduction of the Sheet Metal Cut To Length Machine, designed to meet the highest industry standards.This state-of-the-art machine is designed to effortlessly cut sheet metal with precision and efficiency, saving users time and effort. The advanced automation system guarantees accurate and consistent results, reducing material waste and increasing productivity. The machine is perfect for various industrial applications, including construction, automotive, and manufacturing, combining cutting-edge technology with user-friendly features for an exceptional cutting experience.The Sheet Metal Cut To Length Machine from Wuxi DLS Machinery Co., Ltd. has certainly captured the attention of professionals and industry experts. Its unrivaled flexibility, versatility, and safety features have made it an invaluable asset for those in the metalworking industry. Boasting a user-friendly interface and compact design, the machine ensures ease of operation and convenience, catering to both experienced professionals and beginners alike.The durability of the Sheet Metal Cut To Length Machine is remarkable, as it is built with high-quality materials to withstand the rigors of daily use. It delivers consistent results without compromising on speed or accuracy. Furthermore, the machine incorporates multiple safety mechanisms, including emergency stop buttons and protective guards, providing a secure working environment for operators.The fully automated cutting process dramatically reduces production time while maintaining superior accuracy and quality. This machine streamlines workflow, allowing users to take on more projects and deliver outstanding results to clients. It empowers users to take control of their sheet metal processing needs, enhance their production capabilities, and ultimately, boost business success.Wuxi DLS Machinery Co., Ltd. takes pride in delivering machines that meet the highest industry standards. Their state-of-the-art factory is equipped with the latest machinery and a team of skilled professionals dedicated to crafting exceptional products that revolutionize the way metal is handled and processed.Customer reviews of the Sheet Metal Cut To Length Machine have been overwhelmingly positive, with many describing it as an exceptional tool for all metal fabrication needs. Users have praised its precise and accurate cutting of sheet metal, ease of use, efficiency, and robust construction.In conclusion, Wuxi DLS Machinery Co., Ltd. is setting new standards in the industry with its cutting-edge Sheet Metal Cut To Length Machine. From its innovative design and advanced technology to its unrivaled flexibility and safety features, this machine is a true game-changer for professionals in need of precise and accurate cuts in sheet metal. With its unwavering commitment to excellence and technical innovation, Wuxi DLS Machinery Co., Ltd. has firmly established itself as a leading manufacturer and supplier in China, offering high-quality machines and competitive prices that are revolutionizing the metalworking industry.
High-Quality 6 High Cold Rolling Mill - Wholesale Factory Price
Wuxi DLS Machinery Co., Ltd., situated at the Hongshan Machine Photoelectric Industrial Park in Wuxi Xinwu District, is a prominent force in the manufacturing industry. The company boasts a sprawling area of 20,000 square meters, equipped with over 50 units of various precision machining equipment and large floor type boring machines. With an annual production capacity of over 200 sets and a hoisting capacity of up to three hundred tons for single piece equipment, Wuxi DLS Machinery Co., Ltd. stands as a leader in the industry.Since its establishment in 1985, Wuxi DLS Machinery Co., Ltd. has been unwavering in its commitment to technical research and production practice. The company has focused on developing and producing a wide array of rolling mills, including two roll, four roll, six roll, twelve roll reversing, and twenty roll reversing, as well as continuous rolling mills. This dedication to innovation and quality has solidified the company's position as a leader in the rolling mill manufacturing industry in China.One of the standout products offered by Wuxi DLS Machinery Co., Ltd. is the state-of-the-art 6 High Cold Rolling Mill. This cutting-edge equipment represents a game-changer in the metal manufacturing industry, combining precision, efficiency, and versatility to revolutionize the cold rolling process.The 6 High Cold Rolling Mill is designed with advanced engineering, ensuring exceptional quality and highly precise rolled metal sheets. Its innovative technology guarantees consistent and uniform thickness throughout the entire length, resulting in superior flatness and surface finish. The mill can handle a wide range of materials flawlessly, including stainless steel, aluminum, and various other metals.Notably, the 6 High Cold Rolling Mill offers unparalleled speed and efficiency. Equipped with a powerful motor and finely calibrated components, it can achieve high production rates without compromising on quality. This translates to increased output and reduced production time, making it an ideal solution for businesses looking to enhance their manufacturing capabilities.Moreover, the mill's exceptional versatility allows it to accommodate various sheet sizes and thicknesses, catering to a wide range of applications across diverse industries. From automotive to construction, from household appliances to aerospace, the 6 High Cold Rolling Mill demonstrates its adaptability and efficiency.The commitment to safety and reliability is evident in the inclusion of cutting-edge safety measures and a user-friendly interface, ensuring a smooth and secure operation for operators. The 6 High Cold Rolling Mill truly represents top-of-the-line technology that transforms metal production capabilities, setting businesses apart from the competition.Customer satisfaction is a top priority for Wuxi DLS Machinery Co., Ltd. As such, the company offers competitive wholesale prices without compromising on quality, enabling businesses to elevate their production capabilities with high-performance equipment.The 6 High Cold Rolling Mill has garnered praise and positive feedback from industry professionals, with users touting its game-changing impact on the steel industry. Its precision, efficiency, and robust design ensure high-quality output and exceptional performance, setting it apart from traditional rolling mills. The mill's flexibility and versatility allow for customization, meeting the diverse needs of various industries, while its user-friendly interface and automated features make it a reliable and convenient solution.In conclusion, the 6 High Cold Rolling Mill from Wuxi DLS Machinery Co., Ltd. exemplifies the company's dedication to innovation and excellence. With a focus on delivering top-quality products and driving manufacturing capabilities to new heights, the company continues to solidify its position as a leading manufacturer of rolling mills in China. Businesses looking to enhance their metal production processes can trust in the exceptional performance, efficiency, and versatility offered by the 6 High Cold Rolling Mill.Contact Wuxi DLS Machinery Co., Ltd. today to learn more about this exceptional machinery and explore the possibilities for transforming your business's manufacturing capabilities.